Quality Improvement Activities
Quality Improvement Activities
We strive to maintain and improve quality in order to provide high quality products that our customers can use with confidence.
Efforts from the Production Preparation Stage
We have established approximately 300 check items and conduct internal audits to ensure that each phase of production preparation is properly executed, starting from the production preparation phase to each functional axis (development, production engineering, and factory).
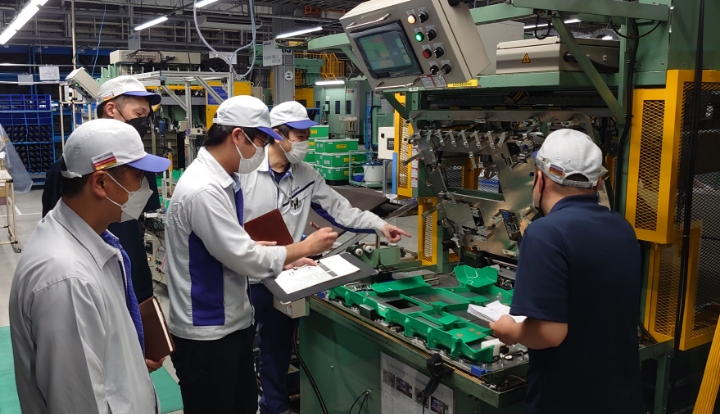
Market Quality Improvement Activities
We collect information from the market (customer requests, defect information, etc.) as quickly as possible, and our development, manufacturing, production engineering, and quality departments work together to quickly implement improvements.
-
01 Recall of parts indicated in the market
Confirm and clarify the actual phenomenon
- ・Gathering of information
- ・Confirmation of complaints and incidents from customers regarding parts pointed out in the market
-
02 Joint analysis within the company
Share information of defect phenomenon, confirmation items and determination of division of roles
- ・Confirm the parts pointed out in the market and share the facts with departments of development, manufacturing, and production engineering
- ・Determination of investigation items and division of roles among departments of development, manufacturing, and production engineering
-
03 Examination and review of proposed countermeasures
Factor analysis, review and study of proposed countermeasures
- ・Identify the cause from analysis of failure factors, test results, and reproducibility checks
- ・Examine proposed countermeasures based on the identified causes, manufacture samples, and confirm their effectiveness through testing, etc.
- ・Agreement and decision on countermeasure plan with departments of development, manufacturing, and production engineering
-
04 Implementation of countermeasures
Incorporation of countermeasures into the process
-
・Application of countermeasures to the process
*Application of countermeasures to the process by modification of molds or addition of work processes, etc.
-
・Application of countermeasures to the process
-
05 Application of modified products
Production of products to which countermeasures are applied
- ・Adoption of countermeasures in the production line
-
06 Deliveries to automobile manufacturers
Supply of modified products to automobile manufacturers
- ・Delivery of modified products to automobile manufacturers
-
07 Prevention of recurrence and sharing of information
Share information about defects and countermeasures with global bases
- ・For manufacturing countermeasures, share information about defects and countermeasures with global bases
- ・For designing countermeasures, incorporate them to the next model
-
・Incorporate them to the technical standards
*Information about countermeasures is input into the quality information system and checked at global bases.
Quality Information Management System: Effective use for prevention and recurrence
We have established a Quality Information Management System (WINGS*1) to learn from the past and incorporate it to future quality improvement process.
This system allows us to share the information about quality management in real time between domestic and overseas bases, and to create an global information infrastructure that enables us to utilize past quality issues in the next model.
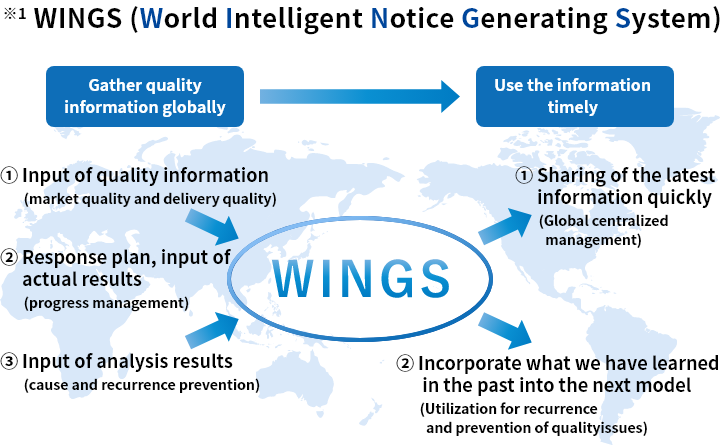